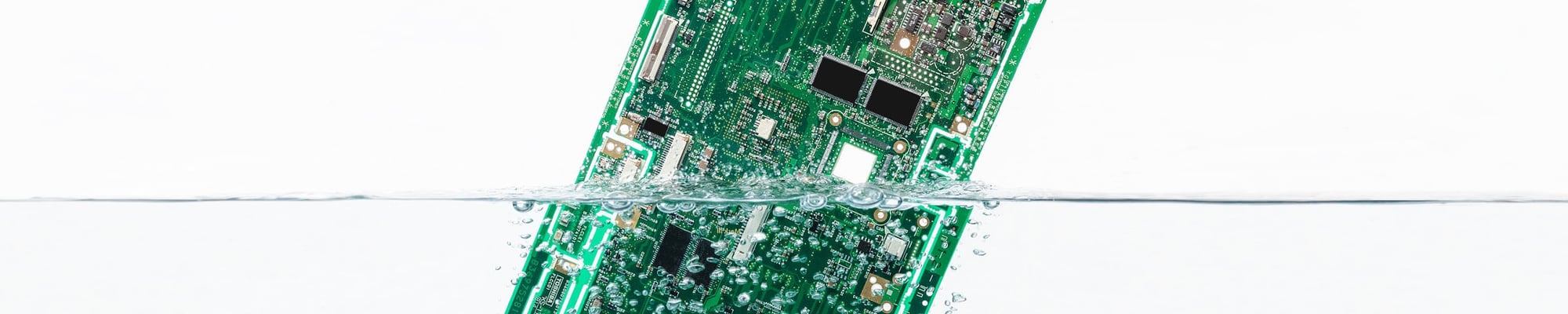
PCB Defluxing and Cleaning
Failure is not an option! When cleaning PCB assemblies, the primary goal is to remove contaminants from populated boards and hybrid circuits resulting from fluxes and improper handling. The use of engineered PCB cleaning solutions is essential to ensure flux residues are fully removed from the assemblies used in high-reliability applications and industries such as automotive, medical, aerospace, and military.
When you are manufacturing electronic circuits that are used in high-reliability applications, field failures resulting from dendritic growth, electrochemical migration, leakage current, and conformal coating among others are unacceptable risks.
2 Top Reasons Your PCBs Could Be Failing:
4 Industry Standards For Cleaning Your PCBs:
Finding the right cleaning product is critical. High precision cleaning requires more than just a chemical solution as today’s printed circuit boards are incredibly challenging to clean.
PCB Cleaning Challenges Are Changing Due To:
- Lower component standoff heights
- Increased board density
- Stacked and complex component types
- Increased use of sensitive materials
At ZESTRON, cleaning agents are powered by technology. We deliver compatible electronics cleaning and defluxing solutions, comprehensive process solutions tailored to your unique needs, and a commitment to providing the latest solutions through our continual investment in R&D.
The result: you can be assured that your cleaning process is optimized to stay ahead of the latest printed circuit board technology.
2 Key Reasons Your PCBs Could Be Failing
When cleaning assemblies (PCB cleaning, PCBA cleaning), the primary goal is to remove resin and flux residues from populated boards and hybrids as well as production-related residues created by handling. Even though in many low-end production processes the use of "no-clean" works well, high-end assemblies that will be employed in industries such as automotive, telecommunications, military, and aerospace, require the use of a specific PCB cleaning agent.
1. Electrochemical Migration (ECM)
Per IPC-TR-476A, ECM is defined as - “The growth of conductive metal filaments or dendrites on or through a printed board under the influence of a DC voltage bias”. Two common ECM mechanisms are:
- Conductive anodic filaments (CAF): migration within a printed circuit board (PCB).
- Dendritic growth: ECM along a surface that produces a dendrite (tree-line) morphology.
Electrochemical Migration On PCB
2. Contamination Induced Leakage Current
For electrical assembly, current leakage in a printed circuit board (PCB) can result in intermittent or permanent failure. Current leakage can occur due to insulation resistance reduction (due to the presence of contamination) between adjacent solder pads on a PCB. This hygroscopically induced moisture absorption phenomenon can for example intensify due to dissociated hydronium ions (i.e. from activators), to further result in malfunction and complete assembly failures.
Leakage Current On PCB
4 Industry Standards For Cleaning Your PCBs
Without addressing the failure mechanisms at key stages throughout the design and manufacturing process, your board reliability may be compromised putting end-product performance at risk. Cleaning the circuit assemblies is a crucial part of any reliability engineering process — proactively mitigating risk by removing the contaminants that lead to field failures.
1. Inline Cleaning Machine
When cleaning electronic assemblies with large production throughputs and minimal component diversity, implementing a spray-in-air inline system can be a time and cost-saving solution. The printed circuit boards are run on an automatic conveyor belt through individual process steps, where cleaning, rinsing, and drying are performed in separate chambers.
Inline Cleaning
2. Batch Cleaning Machine
With a spray-in-air batch system, the cleaning method operates very similarly to the technology used in a dishwasher. All of the process steps are executed in the same process chamber. The cleaning medium is sprayed onto the electronic assemblies through nozzle fittings or rotating spray arms. The cleaning effect is generally not achieved through spray jet pressure, as with inline processes, but rather via the volume of cleaning medium passed over the substrates.
Batch Cleaning
3. Ultrasonic Cleaning Machine
Sound is caused by the propagation of pressure and density fluctuations (compression and rarefaction of molecules) in an elastic medium. Frequencies ranging from 20 Hz to 20 kHz, are audible for humans. Vibrations with frequencies exceeding 20 kHz are called ultrasound.
In the case of cleaning under components and complex geometries, ultrasonic cleaning can be useful since the sound waves are capable of reaching every angle of the mounted circuit board. Many industry cleaning machines have an automatic frequency adjustment for the modulation of the ultrasound (sweep) working frequency, which prevents “hot spots” and allows material-friendly cleaning.
Ultrasonic Cleaning
4. Manual Cleaning
In addition to cleaning PCBs, power modules, stencils, and machine parts in automated cleaning systems, flux residues, particles, SMT adhesives, and solder paste can also be removed manually. Manual cleaning is often a popular alternative if the throughput is low, i.e. when building prototypes, or during electronic component rework/repair.
Manual cleaning can be performed without investing in any equipment. If a production facility with medium/high throughput, several shifts, and requires excellent cleaning results, an automated cleaning process is then preferred.
Manual PCB Cleaning